March Madness for Facility Managers: Why Planning Ahead Wins the Game
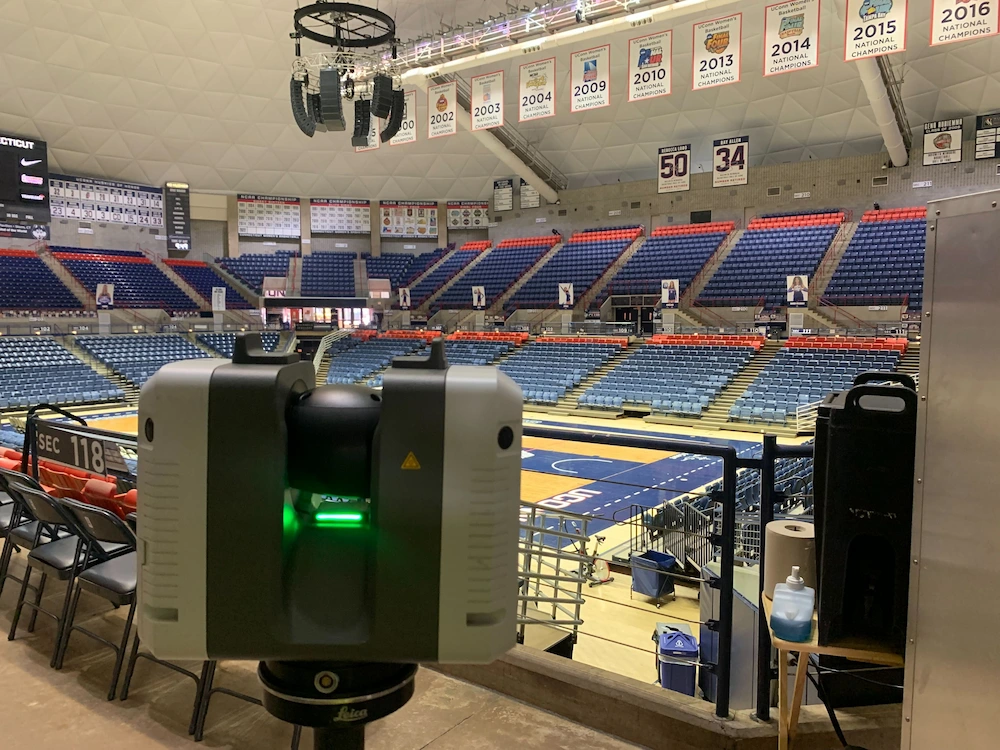
Stay Ahead with Strategy, Precision, and Accurate Data
What makes March Madness so thrilling is its unpredictability. Cinderella teams emerge, top seeds fall unexpectedly, and buzzer-beaters keep fans on the edge of their seats. The key to victory? Preparation, execution, and adaptability – the same principles that apply to facility management.
To stay ahead of the game and avoid any fouls, facility managers must navigate challenges with precision. By combining our services with the expertise of our parent company, GPRS, facility managers gain a comprehensive suite of tools to optimize operations. Together, we provide the data and insights that empower facility managers to come out as champions on the court.
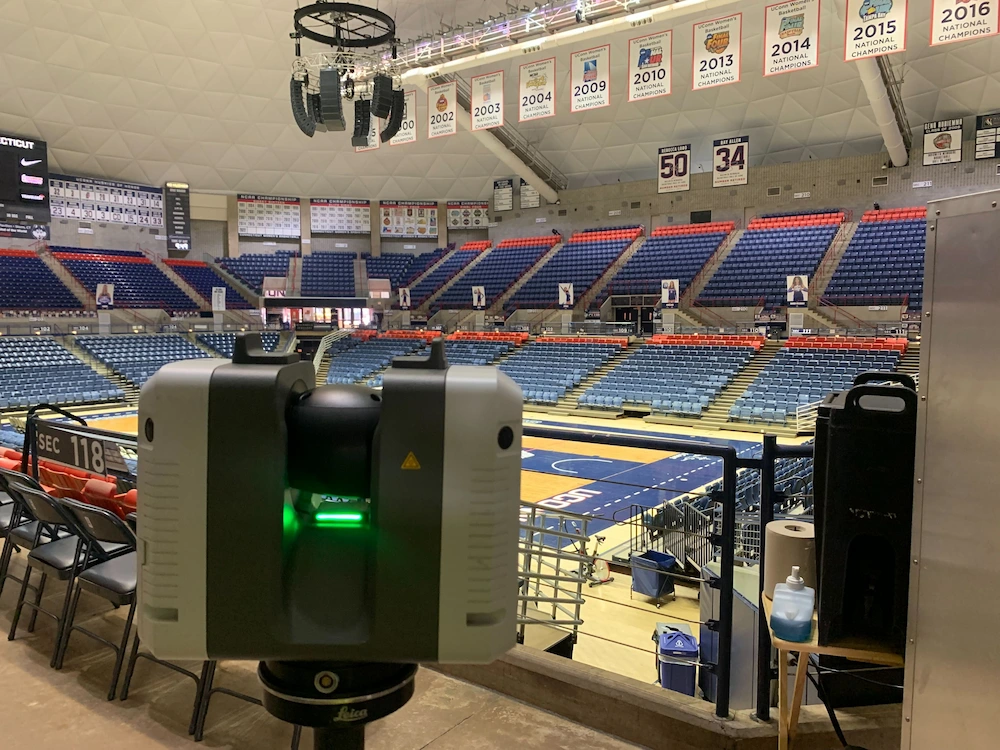
History of March Madness
March Madness, the annual NCAA men’s basketball tournament, has captivated sports fans for decades. The term "March Madness" was first coined in 1939 by Henry V. Porter, an Illinois high school official, to describe the excitement surrounding the state's high school basketball tournament. That same year, the NCAA held its first men's basketball tournament, featuring just eight teams. Over the decades, the tournament has expanded to include 68 teams, with millions of fans filling out brackets and watching the games unfold.
Facility Management and the March Madness Mentality
Facility managers juggle multiple responsibilities, from ensuring smooth daily operations to planning for renovations and unexpected challenges. Much like a basketball coach preparing for a tournament, facility managers must have a game plan based on accurate, up-to-date information.
Scouting Report: The Importance of Data
Just as coaches rely on scouting reports to analyze their opponents, facility managers need precise building data to make informed decisions. Traditional building documentation can be outdated or inaccurate, leading to costly mistakes. That’s where 3D laser scanning comes into play.
For example, our work with Williams College is one of Existing Conditions' largest projects to date. After initially scanning a single building, the college saw the immense value of 3D laser scanning and selected our team to document the entire campus – over four million square feet. The accurate as-built documentation we provided ensured that their facility managers have the data they need for future planning and renovations.
Similarly, Suffield Academy partnered with Existing Conditions and Centerbrook Architects to survey eight buildings, including athletic and performing arts facilities. This project included both interior and exterior documentation, providing 3D Revit floor plans, reflected ceiling plans, exterior elevations, and roof plans – essential tools for their facility management team.
Game Plan: The Role of 3D Laser Scanning
.webp)
3D laser scanning captures millions of data points that are then processed into a point cloud, creating an accurate 3D as-built data set of the site. This all happens very quickly, with some scanners, like our Leica RTC360, capturing and calculating two million points per second with 2-4 mm accuracy. This data serves as the foundation for renovations, maintenance, and asset management.
The Winning Strategy: Benefits of 3D Laser Scanning for Facility Managers
1. Accuracy Wins Championships
In basketball, missing a shot by a fraction of an inch can cost a team the game. Similarly, inaccurate building data can lead to costly errors. 3D laser scanning provides:
· Rapid documentation
· Optimized workflows
· Improved collaboration
2. Speed and Efficiency: Beating the Shot Clock
Teams only have seconds to make plays, and facility managers often work under tight deadlines. Traditional measuring methods can be time-consuming and prone to human error. 3D laser scanning:
· Reduces data collection time from weeks to hours
· Minimizes disruption to building occupants
· Delivers rapid, reliable insights
3. Improved Teamwork and Collaboration
Successful basketball teams thrive on communication and collaboration. Facility managers, architects, engineers, and contractors must work together seamlessly. Accurate as-built documentation ensures:
· Everyone works from the same accurate data
· Reduced miscommunication between stakeholders
· More efficient project coordination
4. Risk Mitigation: Avoiding Costly Turnovers
Turnovers in basketball can change the course of a game, just like unexpected construction surprises can derail a project. With accurate as-built documentation, facility managers can:
· Identify structural issues before renovations begin
· Avoid clashes between new and existing infrastructure
· Reduce costly change orders and delays
5. Cost Savings: Smart Plays for the Budget
Coaches allocate resources carefully to maximize team performance. Similarly, facility managers must balance budgets while ensuring efficiency. 3D laser scanning helps:
· Reduce rework and material waste
· Optimize space utilization
· Streamline maintenance and asset management
6. Future-Proofing Facilities
Winning teams plan for the future, developing young talent, and adjusting strategies. Facility managers must also think ahead, ensuring their buildings are ready for future needs. 3D laser scanning:
· Provides a digital twin of the facility for future reference
· Supports sustainability initiatives by reducing unnecessary renovations
· Helps with long-term asset management and lifecycle planning
Creating Your Facility Management Bracket: How to Get Started with 3D Laser Scanning
1. Assess Your Facility’s Needs
Just as teams evaluate their strengths and weaknesses, facility managers should identify areas where accurate as-built documentation would be most beneficial. Consider:
· Aging buildings with outdated or missing documentation
· Spaces undergoing renovations or expansions
· Critical infrastructure requiring accurate records
2. Choose the Right Technology Partner
Not all 3D laser scanning providers are created equal. Work with experienced professionals who specialize in 3D laser scanning and as-built documentation surveys to ensure high-quality results.
3. Implement and Utilize Data Effectively
Once you have accurate building data, use it to your advantage:
· Use it to plan preventative maintenance
· Share it with architects and contractors for seamless project execution
· Integrate it into SiteMap®
With SiteMap®, GPRS’ proprietary project management platform, you can store and manage your data in a central, cloud-based location. This platform enables teams to access and collaborate on the building data anytime, anywhere. SiteMap® allows facilities managers and other stakeholders to easily visualize, analyze, and share critical information, from reality capture data and subsurface mapping to as-built documentation.
Its interactive interface ensures that everyone involved – whether in architecture, engineering, or construction – have real-time access to the same data, reducing the risk of miscommunication or errors. This seamless sharing of information helps prevent clashes, streamlines decision-making, and keeps projects on schedule, making SiteMap® an invaluable tool for facilities managers looking to improve workflow efficiency and maintain building integrity.
Cut Down the Nets with Accurate Documentation
Winning in March Madness requires preparation, teamwork, and the right strategies – just like successful facility management. By leveraging 3D laser scanning and as-built documentation, facility managers gain a competitive edge, ensuring their buildings are accurately documented, efficiently managed, and prepared for future challenges.
Don’t let outdated information be your bracket-buster. Invest in accurate data today and watch your facility management game reach championship levels.
Contact us today to elevate your facility management strategy.
FAQs
How Does Laser Scanning Work?
One primary method is that a laser scanner sends light pulses at high speeds which reflect off objects and return to the scanners’ sensor. For each pulse, the distance between the scanner and object is measured by determining the elapsed time between the sent and received pulses. Each point of the scan will be converted to a pixel with a known x-, y-, and z- coordinate. Laser scans or LiDAR scans are taken in multiple positions around a site from varying viewpoints. Millions of data points are captured and processed into a point cloud, creating an accurate data set of the structure or site.
What strategies can facility managers use to manage energy consumption and improve sustainability?
- Energy Audits: Conduct audits to identify inefficiencies and improvement opportunities.
- Energy-Efficient Upgrades: Install energy-saving technologies, such as LED lighting and smart controls.
- Renewable Energy: Utilize renewable sources like solar panels to reduce energy dependency.
- Behavioral Changes: Encourage occupants to adopt energy-saving behaviors.
- Sustainability Programs: Implement waste reduction, water conservation, and sustainable procurement.
- Monitoring and Analytics: Leverage analytics to track energy usage and optimize performance.
What are the Benefits of 3D Laser Scanning?
3D laser scanning captures millions of 3D data points per second for each scan location, providing incredibly rich data of a building or project site. Sites are captured in high detail the first time, eliminating disruption and the need for return visits. Datasets are dimensionally accurate, measurable and shareable, expediting project planning and execution. Accurate design plans are produced from the start expediting field work and reducing change orders, delays and costs. Communication is improved, teams can discuss plans while each has access to the same information, creating a more dynamic working environment.