Why Virtual Design and Construction Matters in AEC
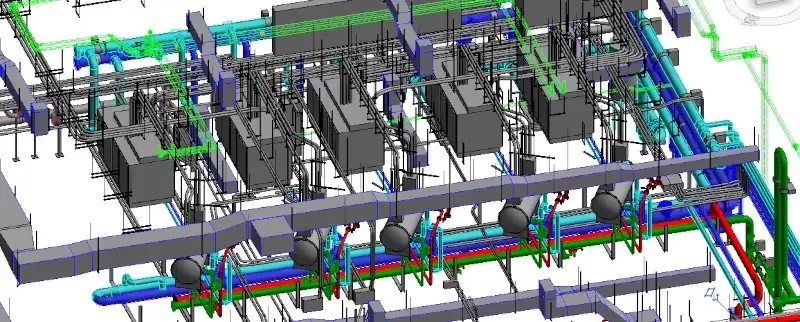
Virtual Design and Construction vs. Virtual Design Consultant
What is Virtual Design and Construction?
According to Stanford University, Virtual Design and Construction (VDC) is a way to use 3D models to plan building projects before construction starts, helping teams work more efficiently. VDC was created in 2001 by Professor Martin Fischer, who leads the Center for Integrated Facility Engineering at Stanford University.
VDC starts by using 3D laser scanners to capture the construction site. These scanners collect very accurate data, down to the millimeter, and turn it into a point cloud. That point cloud is then used to build a smart 3D model called a Building Information Model (BIM).
Design teams use models for the structure, architecture, plumbing, electrical systems, and even underground utilities to plan the project in a digital space. They can test how the project will be built, check for problems where parts might clash, and figure out the best order to do the work. This helps save time, avoid mistakes, and manage costs more effectively.
What is a Virtual Design Consultant?
A blog post on Twenty Third by Deanne describes a virtual interior design consultant, on the other hand, as a professional who uses digital tools and technology to create, plan, and advise interior designs for spaces, often working remotely and presenting concepts through virtual platforms. This is what most people commonly associate with the acronym VDC, though it refers to Virtual Design and Construction in the AEC industry.
In the context of interior design, however, a Virtual Design Consultant represents a new wave of creative professionals who are redefining how design services are delivered. By embracing technology, they offer a flexible, accessible, and often more affordable alternative to traditional in-person design consultations.
How 2D CAD Drawings Are Created
Before VDC became common, building industry professionals used paper-based documents like 2D CAD drawings, printed plans, and spreadsheets. These were often made by hand-measuring buildings with tape measures. This job usually needed at least two people, was time-consuming, and required careful use of tools, great memory, and accurate notetaking. Even with all that effort, it was nearly impossible to get perfect results.
Sometimes, old blueprints are available and can be turned into CAD drawings. To do this, someone must carefully copy the measurements from a PDF floor plan, including room sizes, wall thickness, and system parts. These details are important for planning changes to a building, but mistakes can happen easily when copying by hand. However, blueprints are documents of what the structure was intended to be, not necessarily how it was finally constructed.
Making a full set of 2D CAD drawings is prolonged. Depending on how big or complex the project scope is, it can take weeks or even months. If any design changes happen, they must be updated by hand and shared with the team, which can slow the timeline down and impact productivity.
Another big disadvantage with traditional CAD methods is that the measurements used to make them aren’t always correct. Even when using laser tools like DISTOs, the numbers can be off by as much as a foot. This margin of error forces general contractors to include schedule buffers and budget contingencies to accommodate change orders and rework during construction.
A 2022 report in Engineering News-Record stated that mistakes like these cost the construction industry up to $177.5 billion each year in lost labor. It also found that workers lose about two full days every week fixing errors.
Virtual design and construction provide a more efficient way to reduce/plan for/and manage unexpected clashes because it uses tools like 3D laser scanning, BIM, and digital twins to create accurate digital models of real spaces. BIM models help project teams plan, build, and manage projects more effectively throughout its entire lifecycle.
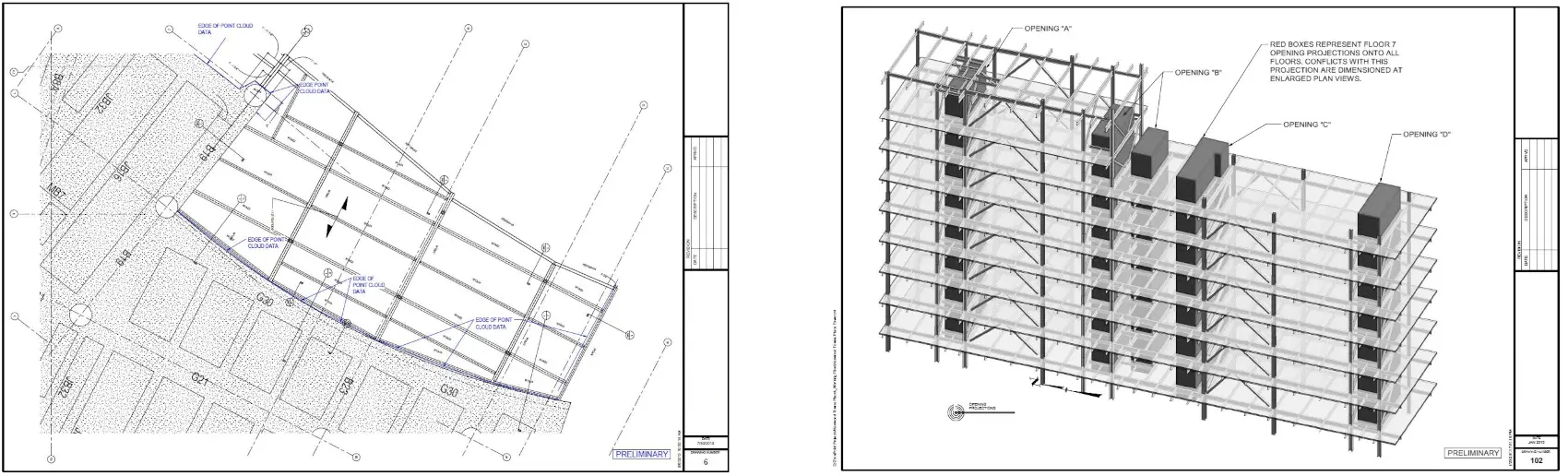
How a BIM Model is Created
A Building Information Model (BIM) is a data-rich, three-dimensional digital representation of a physical structure. It integrates detailed information about the building’s geometry, systems, and components, making it a critical tool for Virtual Design and Construction (VDC) workflows. BIM models enable project teams to collaborate effectively, coordinate design intent, and plan construction sequencing in a shared digital environment.
To create a BIM model, the first step is to document the building or site using 3D laser scanning. This method uses LiDAR (Light Detection and Ranging) to collect millions of tiny data points that show the exact shape and size of the space. The result is a very accurate virtual representation of the real-world site, called a digital twin.
BIM models and digital twins are both 3D models, but they are used in different ways. BIM models focus on how the building is built and how its systems work together. Digital twins focus more on how teams use the space and how it functions over time. BIM is used for planning and building, while digital twins are used for viewing and analyzing the space.
3D laser scanning is the most powerful way to collect accurate information about a building, both above and below-ground. It captures the size, shape, and layout of everything in the space.
For example, Existing Conditions’ 3D laser scanning can measure with 2-4 mm accuracy, which helps teams mitigate risks and view clashes before construction starts. Underground utilities like water, sewer, gas, electric, and cable lines can be found by our parent company, GPRS, using tools like Ground Penetrating Radar (GPR) and Electromagnetic Induction (EMI).
All above and below ground data can be turned into a full BIM model using software like Autodesk Revit. These models show everything structural to architectural details, MEP (mechanical, electrical, and plumbing) components to locating utilities.
According to Stanford University’s Center for Integrated Facility Engineering, BIM adoption yields measurable benefits. Based on data from 32 major projects, the reported outcomes include:
- Up to 40% reduction in unbudgeted changes
- Cost estimation accuracy within 3% compared to traditional methods
- Up to 80% faster cost estimation
- Savings of up to 10% of contract value through clash detection
- Up to 7% reduction in total project duration
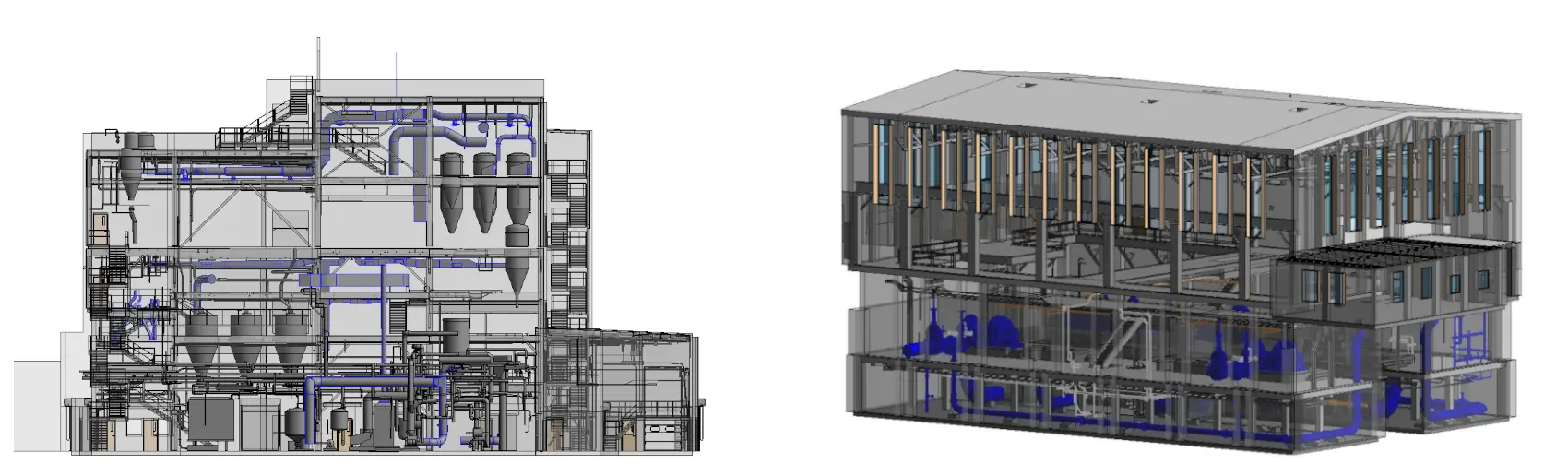
What You Should Know About BIM vs. VDC
BIM is a structured process for creating and managing a digital representation of a physical building. It integrates both geometric and non-geometric data into a centralized model.
VDC is a wider process that includes BIM but also uses other digital tools. VDC helps teams plan, design, build, and manage a building from start to finish. While BIM is a key part of VDC, VDC goes beyond just modeling.
VDC can also include tools like 3D laser scanning, point cloud data, and simulation software.
How Virtual Design and Construction Helps Building Projects
Virtual Design and Construction helps construction teams with coordination and avoid change orders to keep projects running on time, on budget, and safe.
The 3D BIM model used in VDC provides several advantages:
- Expedited design decisions using real-time digital data
- More accurate project planning, which helps reduce costs
- Clear understanding of the project for all team members and subcontractors
- Streamlined sharing of design updates, so everyone stays informed
- Early detection of safety hazards, before construction begins
- Increased coordination between all parts of the project team
Who Benefits from Virtual Design and Construction?
Virtual Design and Construction is used by professionals in the AEC industry professionals to plan, visualize, and manage building projects before construction begins.
These stakeholders use VDC:
- Architects
- Engineers
- Contractors
- Owners and Clients
- Project Managers
- Facility Managers
- Construction Consultants
- Government and Regulatory Authorities
- Manufacturers and Suppliers
- Educational Institutions
VDC digitally maps the construction process prior to physical execution, enabling early-stage collaboration among project stakeholders. By leveraging intelligent 3D BIM models, AEC professionals can proactively identify and mitigate design and coordination risks, significantly reducing the likelihood of costly rework and schedule delays.
How Companies Use Virtual Design and Construction
Stanford University researchers emphasize that Virtual Design and Construction VDC is a critical tool for managing complex infrastructure and building projects. According to their findings, VDC workflows enhance project efficiency, increase reliability, and mitigate common risks. Teams are leveraging VDC to streamline the assessment and documentation of existing conditions, integrating these insights into design, construction, and operational strategies.
Key applications include:
Construction Documentation: High-fidelity 3D BIM models are developed to represent architectural, structural, MEP, and utility systems as they exist on-site. These models are generated using advanced software platforms that enable multidisciplinary teams to collaborate within a unified digital workspace.
Integrated Data Environments: VDC extends beyond geometric modeling by incorporating diverse datasets which include historical records, material specifications, cost data, and scheduling inputs, into a centralized digital framework.
Stakeholder Coordination: VDC facilitates real-time collaboration among architects, engineers, contractors, and owners. Shared access to the digital model enhances communication and coordination, particularly when validating or updating existing site conditions.
Virtual Visualization of Existing Assets: Stakeholders can interact with the digital environment to visualize current site conditions. This capability supports the early identification of spatial conflicts, informs design decisions, and optimizes construction planning.
Performance Simulation and Analysis: Existing condition models are used to simulate structural behavior, energy performance, and system efficiency. These analyses inform retrofit strategies and validate design assumptions against real-world constraints.
Clash Detection: VDC tools identify spatial conflicts between existing and proposed building systems, which include mechanical runs intersecting with structural elements, prior to construction. Early detection prevents rework and cost overruns.
Prefabrication: Accurate as-built data supports the off-site fabrication of components, ensuring compatibility with existing structures and minimizing on-site adjustments.
Cost and Budget Management: VDC enables precise cost estimation based on verified existing conditions. This supports budget control and financial planning throughout the project lifecycle.
Schedule Optimization: By incorporating verified site data into construction sequencing, VDC enhances schedule accuracy and supports more efficient resource allocation.
Facility Management: Upon project completion, the digital model, enriched with verified existing conditions, serves as an asset for facility managers. It supports maintenance planning, system upgrades, and long-term operations.
What Role Does Existing Conditions Play in Virtual Design and Construction?
Over the past 27 years, Existing Conditions has measured, documented, and modeled over 10,000 buildings spanning over 700 million square feet across the United States, establishing ourselves as an industry leader in 3D laser scanning.
Before any design or construction work begins, you need to have situational awareness of what is already on-site. This includes the layout of the building, the location of structural elements, and the condition of mechanical, electrical, and plumbing systems. By partnering with a 3D laser scanning company, teams can receive this information with high accuracy which becomes the foundation for all future planning.
These models also help you avoid costly mistakes. For example, if a new design includes a beam or pipe that would interfere with something already in place, the clash can be spotted and fixed in the digital model before construction starts. This saves time, reduces rework, and helps keep the project on schedule and within budget. It also improves communication between architects, engineers, and contractors, since everyone is working from the same sheet of music.
Beyond construction, accurate 3D BIM models are useful after the project is complete. You can use them to locate systems, plan maintenance, and make upgrades more efficiently. In short, accurate as-builts are not just a starting point, they are a critical part of the entire VDC process, from design through construction and into long-term building management.
What is Virtual Design and Construction?
VDC enables project teams to collaborate effectively from the earliest stages of a project. By planning in a digital environment before any physical work begins, stakeholders, including owners, designers, contractors, and subcontractors can evaluate design options, construction methods, and material selections.
Existing Conditions provides accurate point clouds, as-built drawings, and 3D BIM models for virtual design and construction to help you start accurate and stay accurate.
Architects, builders, engineers, developers, and facility managers, trust us to deliver digital representations of the as-built environment with unparalleled accuracy and efficiency. Our services, including 3D laser scanning and BIM modeling, enable architects to make informed design decisions based on the most accurate data available.
What can we help you visualize?
FAQs
What are the Benefits of 3D Laser Scanning?
3D laser scanning captures millions of 3D data points per second for each scan location, providing incredibly rich data of a building or project site. Sites are captured in high detail the first time, eliminating disruption and the need for return visits. Datasets are dimensionally accurate, measurable and shareable, expediting project planning and execution. Accurate design plans are produced from the start expediting field work and reducing change orders, delays and costs. Communication is improved, teams can discuss plans while each has access to the same information, creating a more dynamic working environment.
What is a 3D BIM Model?
A building information model (BIM) is a digital representation of the physical and functional characteristics of a building or infrastructure project. BIM stores all the information about a building's life cycle in one place, including design, construction, and operational data, which can be used for planning, renovation, and maintenance. It provides accurate spatial relationships and manufacturer details, as well as geographic information and other pertinent aspects of the building.
What is a Point Cloud?
A point cloud is a collection of data points in a 3D coordinate system, where each point represents a specific location on the surface of an object, essentially creating a digital 3D representation of that object; typically generated using a 3D laser scanner or 3D photogrammetry, with each point containing its own X, Y, and Z coordinate.